Making sure the quality of the product you produce in the lingerie supply chain is important to keep your brand strong, because people expect perfection. If you have ripped seams, irritating fabrics, or bras that stretch out after a few wears, you are gonna have bad reviews, high return rates, and lose repeat customers. We offer a ten-point quality control process at Xiesheng designed to prevent these types of problems and make sure your brand consistently delivers quality products; that way, your brand stays strong, your image stays strong, and so does your customers.
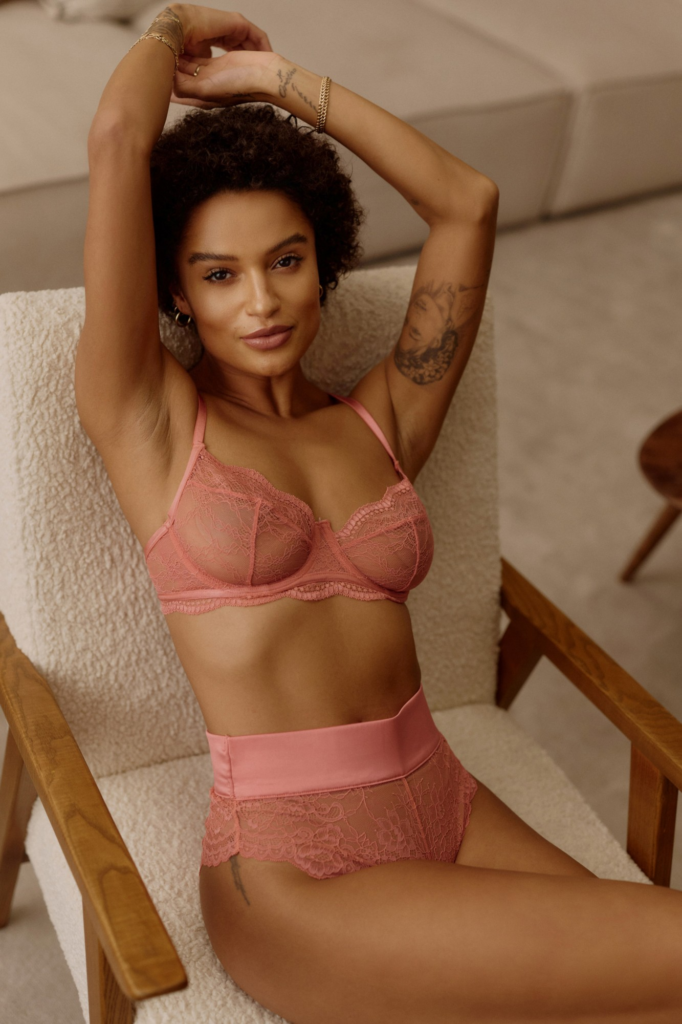
The Critical Role of Material Selection
Picking out the right fabric is key to having good lingerie. Lingerie is up against your skin, and if the fabric doesn’t feel good, or worse yet, is irritating or uncomfortable, people are going to be pissed. Even worse than that, if you have cheap fabrics that change shape after a couple of washes, it ain’t long before you’ll have some complaints and some refunds.
At Xiesheng, we provide fabrics that are soft and feel good on the skin. All of our fabrics are OEKO-TEX certified, which means there are no chemicals in there that’ll get people irritated or would create an allergy. Imagine if people started getting a rash, or worse yet, having an allergic reaction to your cheap fabrics. Forget about how that’ll screw up your reputation; just think about how lawyers do.
Furthermore, we have organic and recycled fabrics for those brands that want to be sustainable and cater to customers who really care about the environment. These fabrics feel good, and they are built to last, even after multiple washes. You run the risk of stretching out the bras or tearing the lace bodysuits if you go with the wrong stuff. That is gonna piss off your customers.
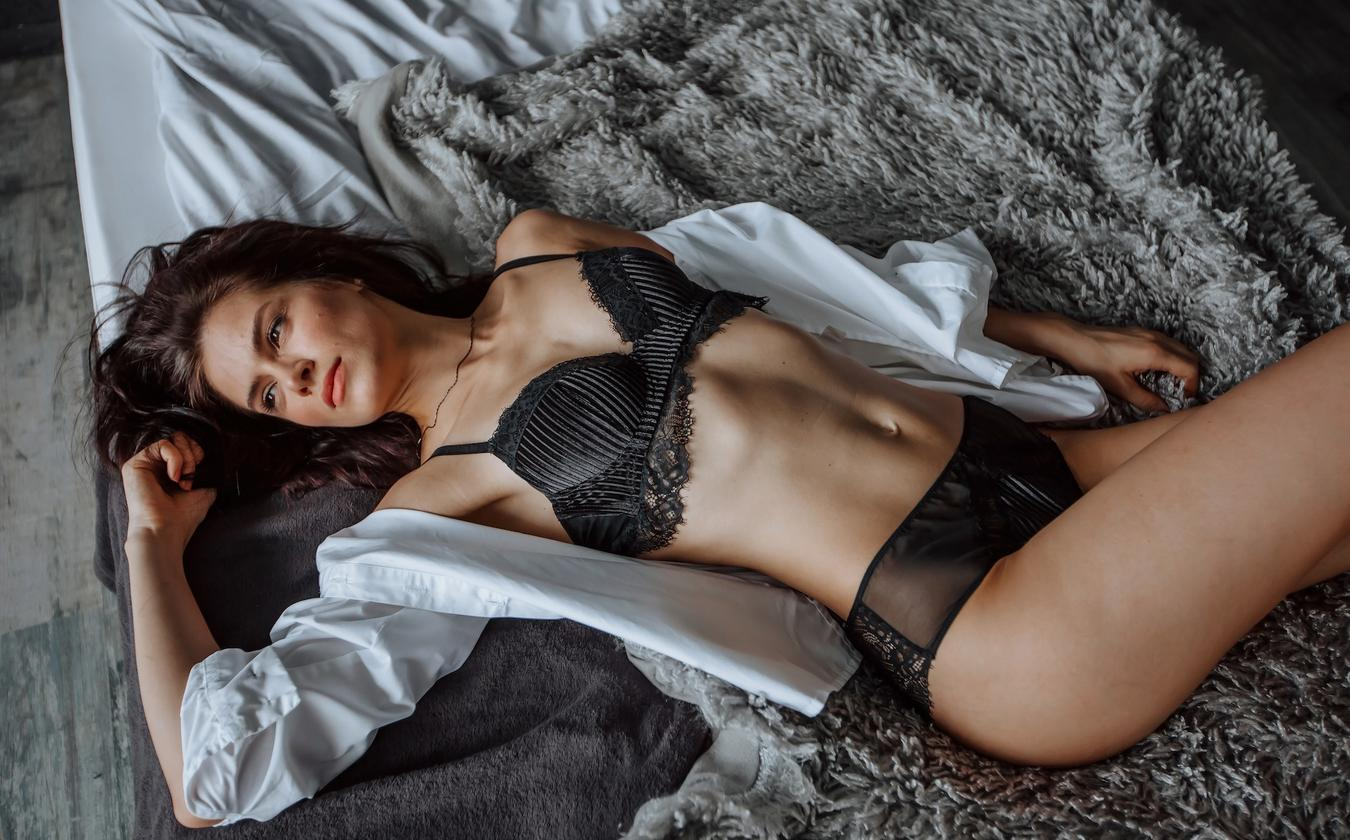
Standardized Production Processes for Reliable Outcomes
Even if you get your fabrics dialed in, if you don’t have consistent production, you’re screwed. Imagine this: your customer orders the same bra, and one size fits great, but the other has seams that pull, or the elastic digs in your skin. These quality differences will kill you.
At Xiesheng, I have dictated standard manufacturing processes in my 10,000m² facility, so that you get a consistent product no matter what size or style you order. I achieve this with advanced machinery and automation—machines don’t get tired or sloppy, which cuts out human error and allows us to be consistent on large orders.

But even having those things in place isn’t enough. We also have skilled workers who oversee and adjust each production line. For example, on our seamless bra lines, our knitting machines have precision, so that every bra fits right and holds up without seams that rub you the wrong way.
Can you imagine if we sent you a bra that had fabric clumps in the knitting or that didn’t fit right because of poor manufacturing? You would send it back, you’d ask for a refund, and you would write bad reviews about me. I don’t want any bad reviews.
That’s why I have strict manufacturing so you don’t wind up with a bra or bodysuit or set of lingerie that wasn’t made exactly right, keeping your customers so happy they become hardcore, long-term fans.
Layered Quality Control Mechanisms
Making sure the quality of the product you produce in the lingerie supply chain is important to keep your brand strong, because people expect perfection. If you have ripped seams, irritating fabrics, or bras that stretch out after a few wears, you are gonna have bad reviews, high return rates, and lose repeat customers. We offer a ten-point quality control process at Xiesheng designed to prevent these types of problems and make sure your brand consistently delivers quality products; that way, your brand stays strong, your image stays strong, and so does your customers.

Pre-Production Inspection: The first thing we do is look at the materials when they come in to make sure there are no defects. If you skip this step, you might have a whole bunch of bras made from fabric that sucks, you give them to people, and three days later, they say, “This is the most uncomfortable bra I’ve ever worn, and the fabric is starting to fall apart.”
In-Line Production Monitoring: The second thing we do is we look over the bras as we’re manufacturing them. We make sure the stitching is strong, the seams are strong, and the sizes are good. What happens if you got a batch of bras coming through, you’re making them, and, “Oh, crap, we didn’t sew this correctly. These seams are weak”?
Post-Production Inspection: The last part of my process is random sampling, where we take the bras after they’re done, just like your customers would get them after a couple of wears and a couple of washes. What happens if we give you a couple of bras, you go to put it on, you wash it one time, and it’s loose? “We just started mass producing a brassiere, and we just screwed up the next six months’ worth of inventory.”
With my three-step process, we make sure you don’t have any problems with the final product when you get it on people. If you skip one of these three things, you let a whole batch of product slip through—and you’re gonna have a horrible time.
Pre-Shipment Inspection and Packaging Quality
Even though the panties are made, you still can’t release them at that point. You don’t want to have an entire shipment of products come in damaged or mislabeled. If the packaging is bad, the products have wrinkles or are not the right sizes. You don’t want to have to deal with unruly customers or sue your supplier.
In the final phase of production at Xiesheng, we do a final inspection before we release any product to make sure everything is perfect. We check the size. We make sure the packaging is right. We make sure the product is labeled appropriately. Could you imagine customers being mad because they got the wrong size? Could you imagine a customer getting a bra that is all wrinkled up and they can’t sell it? Now you have a headache.
In addition to that, we also offer special custom packaging so it looks good when she opens your gift. No matter how nice you are, if she opens your gift and the packaging stinks, it’s not good. You want total control about how your products are presented to the world. You want it to look like your brand. You want it to fit your image. I believe that’s one of the reasons Nick saves a lot of his products he orders. He realizes that this is a big deal. You have to nail everything when it comes to women and relationships. Trust me!
The Strategic Benefits of Partnering with Xiesheng
When you’re picking a panty supplier, you’re not getting someone who’s going to fill an order for you. You’re getting somebody that you’re going to do business with, long-term. This person is going to be responsible for your brand. You haven’t heard me say this yet in this podcast, but how many of you know that if you use the wrong vendor, you will be broke? You can go and fill your store up with panties and 85% of them are going to come back. Everybody’s going to be pissed off by the July 4th, your account with Amazon is going to be shut down by the end of the summer, and you’re going to be at work next summer instead of taking the whole summer off.
That’s serious y’all. So many women I’ve met have told me, “I started this business and I worked my tail off for two years, Ellen. Then I ran out of money because I picked the wrong vendor and I couldn’t recover from it.” I’m hearin’ you, sister, and I don’t want that to happen to you.
At Xiesheng, we consider ourselves partners with you in your journey. We keep you updated on what’s happening every step of the way and we’re there for you all the time. We’re not going to produce something without your permission without you knowing about it, any more than I would create a color in our legwear business without getting an OK from the running store chain that we sold it to. We’ll keep you informed. We’ll tell you where we are. We’ll tell you about quality checks, production times, what’s going on, and where your garments are in the ocean.
Not only do we have all of these great credentials, but we have lots of certifications. We’re an ISO9000 factory and we have an OEKO-TEX rating. We have all of these certifications to make sure that the product is safe, but also that it’s manufactured to a really high standard. We want to make sure everything is done correctly. We have all of these tools in place to protect your brand.
Then the last thing we do that none of the other factories are equipped to do is we’ll do your customization for you. We’ll make stuff for your brand. If you want to make something in a limited edition, we can do that. We can make products that reflect who you are. If you’re making products for your core line and you want to make sure everything matches up, we can take care of that. We can make sure everything matches up with your brand. It all has to be right.
Conclusion
Product quality isn’t just a box to check off—it’s the cornerstone of your brand’s success. Poorly made lingerie leads to customer dissatisfaction, returns, and a damaged brand reputation. At Xiesheng, we take quality control seriously, from material selection to pre-shipment inspections, so you don’t have to worry about these issues.
By partnering with us, you’re not just investing in a supplier; you’re investing in the longevity of your brand. Our rigorous quality control processes, real-time communication, and international certifications make sure you get what you expect—every time. Don't leave your brand’s future to chance. Choose a partner that prioritizes your success just as much as you do.
Reference link:
What You Should Ask a Lingerie Manufacturer
Underwear and Lingerie Quality Management