You launch your clothing line, only to be barraged with customer complaints about quality, which leads to returns, which, in turn, leads to a terrible reputation and loss of sales. This isn’t a hypothetical situation—it’s what actually happens in the apparel industry all the time. You can avoid it, though, with a great quality control program. Quality control is a big deal that’s essential to your success. It’s what’s going to protect your reputation, keep your customers loyal, and make you money. Come on, girls. If you don’t operate this way, you’re going to have to pay a whole lot of money to take back all of these clothes. It’s going to earn you a lot more loyalty from your customers if you make sure everything fits good, feels good, and looks good. And it’ll keep you from having to take back clothes.

The Stakes: Why Quality Control Is Crucial in Apparel Manufacturing
In fashion and in business, the difference between making it and going under can come down to the quality of your product. A 2023 McKinsey survey found that 78% of consumers polled are less likely to buy from a brand after having a bad quality experience with one of their products. For fashion brands, this is important because customers hopping in and out of your business is bad for long-term sustainability.
But, besides just the immediate loss in dollars from returns and refunds, low-quality garments destroy your brand’s long-term reputation. In a world where consumers have more choices than they know what to do with, the last thing they’re going to tolerate is garments that just don’t meet their expectations.
This is especially true if you’re going to be in the premium, specialized, luxury segment where customers demand high-quality garments.
Key Elements of Effective Quality Control
Effective quality control in apparel manufacturing involves several key elements:
- Material Inspection: Quality starts with the raw materials. Before production even begins, every fabric and accessory is inspected for defects and tested for durability, colorfastness, and comfort.
- In-Process Monitoring: At every stage of production, from cutting and sewing to finishing, we monitor the process to catch any issues early. This real-time oversight helps in maintaining consistency and preventing small problems from escalating.
- Final Product Inspection: Once the garments are completed, they undergo a thorough inspection. This includes checking the stitching, sizing, and overall appearance to ensure that each item meets the brand's specifications.
- Feedback Loop: Continuous improvement is a key part of quality control. Feedback from inspections and customer reviews is used to refine our processes and prevent recurring issues.
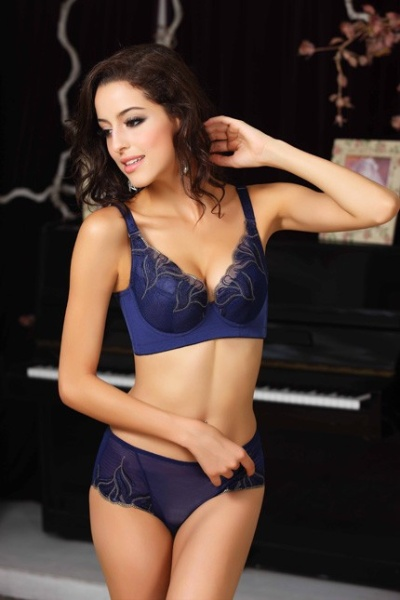
The Role of Certifications and Standards
Certifications like ISO9000, BSCI, and OEKO-TEX are not just badges of honor; they are assurances of quality and safety. For businesses that care about their reputation and want to ensure customer satisfaction, these certifications are non-negotiable. They guarantee that the products are not only well-made but also safe and sustainable.
At Xiesheng, we are proud to hold multiple certifications, which testify to our commitment to quality. These certifications also make it easier for our clients to trust us, knowing that our products meet the highest international standards.
How Technology Enhances Quality Control
Technology plays a vital role in modern quality control. Automated inspection systems, data analytics, and AI-driven quality prediction tools are transforming how manufacturers maintain and improve quality. For instance, real-time data from production lines can help identify trends or issues that might lead to defects, allowing for immediate corrective action.
Incorporating these technologies at Xiesheng has allowed us to minimize errors, reduce waste, and ensure that our products consistently meet customer expectations.
Cost Implications of Quality Failures
The cost of poor quality can be staggering. Beyond the direct costs of returns and repairs, there are hidden costs such as lost sales, damaged reputation, and the potential loss of long-term customers. According to a report by the Harvard Business Review, companies can lose up to 20% of revenue due to quality-related issues.
Investing in quality control, therefore, is not just a cost; it's a strategic investment. It protects your brand, enhances customer satisfaction, and ultimately drives profitability.
Best Practices for Implementing Quality Control
Implementing effective quality control involves several best practices:
- Training and Development: Ensure that your workforce is skilled and knowledgeable about the latest quality standards and techniques.
- Standardized Procedures: Develop and adhere to standardized operating procedures to maintain consistency across production lines.
- Regular Audits: Conduct regular audits of your processes and products to identify areas for improvement.
- Customer Feedback: Use customer feedback as a critical input for quality improvement efforts.
Conclusion: Quality Control as a Competitive Advantage
In the clothing world, you don’t get brownie point, you don’t get the advantage, you don’t get a gold star, and the garden nobody cares about your factory being perfect. But in the apparel world, quality is your advantage. Most people in this business are constipated thinkers who have not figured out how important quality control is. Your job is to be the quality control in the company.
In our factory, we’re stingy with money and generous with quality control. I have a guy in China who manages quality control. We know our quality control guy’s kids. We’ve been to his house. We’ve met his wife.
You don’t have to start with a 100-point inspector. In a perfect world, maybe, but who knows.
It was a small decision to decide to buy production equipment and have people in America do your inspection.